Undergraduates Compete at Design Day with Additive Manufacturing Project
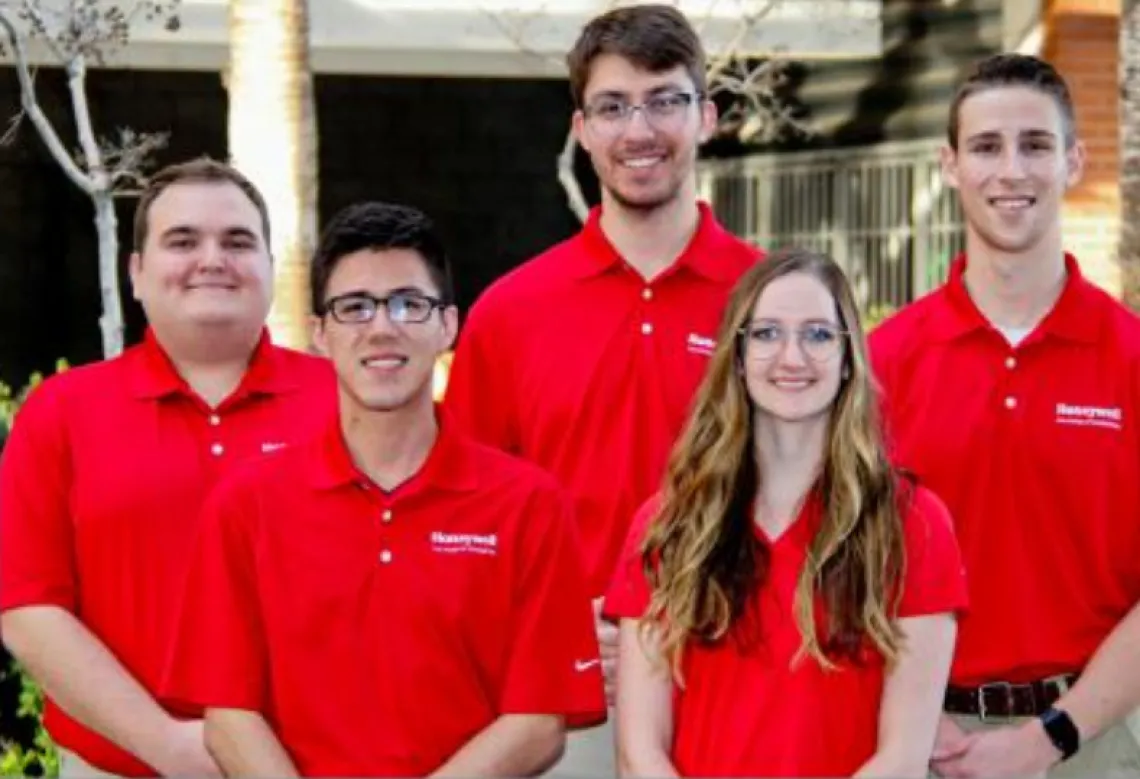
Students from Materials Science & Engineering (Lucas Stolberg, Morgan Swanson, Kathleen van Atta), Mechanical Engineering (Juan Carlos Martinez, Zachary Ondrejka), and Industrial Engineering (Zachary Minnick) teamed on "Additive Manufacturing Process and Dimensional Control" to compete at Design Day 2019. The project mentor and financial support was provided by Honeywell Aerospace.
Direct metal laser sintering offers many advantages over traditional casting and forming processes because it can produce complex geometries using materials that cool rapidly due to their specific microstructure and properties. During printing, however, large temperature gradients can develop and cause distortions that render parts unusable for aerospace applications. Alloy selection, build orientation, support structures, layer thickness, and precompensation for distortion were considered in the design of experiments. After an extensive literature search and multilevel, multivariable design of experiments, Inconel 718, a high-temperature alloy powder, was chosen for the print prototype.
The part, a turbine blade, was scanned using blue light interferometry to compare simulated results with a physical print. Metallurgical analysis was performed to evaluate the material properties and microstructure achieved during the printing process.
A strong correlation was found between the simulated distortion and the actual distortion of the printed part, indicating that dimensional control in additive manufacturing can be achieved using computer simulation and careful alloy selection.